To meet the dramatic increase in domestic semiconductor production envisioned by lawmakers in the CHIPS Act, there will first need to be a dramatic increase in the number of semiconductor workers. How many? Give or take 236,878.
This number comes from the newest Lightcast report Rebuilding Our Semiconductor Workforce: Making the Most of the CHIPS Act. Assuming a domestic doubling from 12% of all global production to 24%, the report examines the skill demand and how educators, businesses, and communities can meet that demand.
Additionally, the CHIPS Act is both a long- and near-term endeavor. Some communities will need time to develop training and methods for redeploying their workforce. Others may be in a position to capitalize now.
What is the CHIPS Act?
Officially the Creating Helpful Incentives to Produce Semiconductors and Science Act, the CHIPS Act was passed in August 2022 to jumpstart the US semiconductor industry. The bill directs $280 billion in spending over the next ten years. Of particular note for communities is the $52.7 billion specifically for semiconductor research, development, manufacturing, and associated workforce development.
This investment will result in major semiconductor job demand throughout the mid- to late-2020s—and perhaps even longer. The US Department of Commerce will administer $50 billion over five years with the aim of expanding domestic semiconductor production.
Who’s ready now?
All site selection decisions involve a myriad of factors. But for years an ample and available workforce has been a primary, if not the primary factor. In 2022 however, demographic trends and a complex economic environment combined to create the tightest job market in history. Consequently, it’s only getting harder to find talent.
But the new plants, expansion of existing ones, and increased supplier activity will have to go somewhere. To answer the question of which regions have the local workforces that are best prepared to produce semiconductors now, Lightcast created a metric called the Regional Labor Force Readiness Score. The score measures readiness in terms of workers either available now or ready to reskill in the most highly demanded and undersupplied semiconductor jobs.
While the score is calculated on an average within each component, excelling at one aspect can help an MSA rank highly. For example:
The Portland, Oregon, area scored highly because it has a large number of workers in semiconductor occupations that will be in high demand (including Computer Hardware Engineers, Architectural and Engineering Managers, and Electrical and Electronic Engineering Technologists and Technicians).
The San Jose area scored highly because it has a large number of workers available for the semiconductor occupations with the greatest demand (including Semiconductor Processing Technicians, Software Developers, and Industrial Engineers).
The Detroit area scored highly due to the number of similarly skilled workers that could be reskilled into relevant occupations (including Commercial and Industrial Designers, Mechanical Engineering Technologists and Calibration Technologists).
Understanding the demand for semiconductors
In 1990, the US produced 37% of the world’s semiconductors. Today, just 12%. Doubling from 12% of all global production to 24% would be a huge step forward and would dramatically mitigate the vulnerability in production, access, and security that currently mark semiconductor manufacturing. While production workers make up a large share of the need to meet this demand (29%), Architecture and Engineering along with Management are also significant needs.
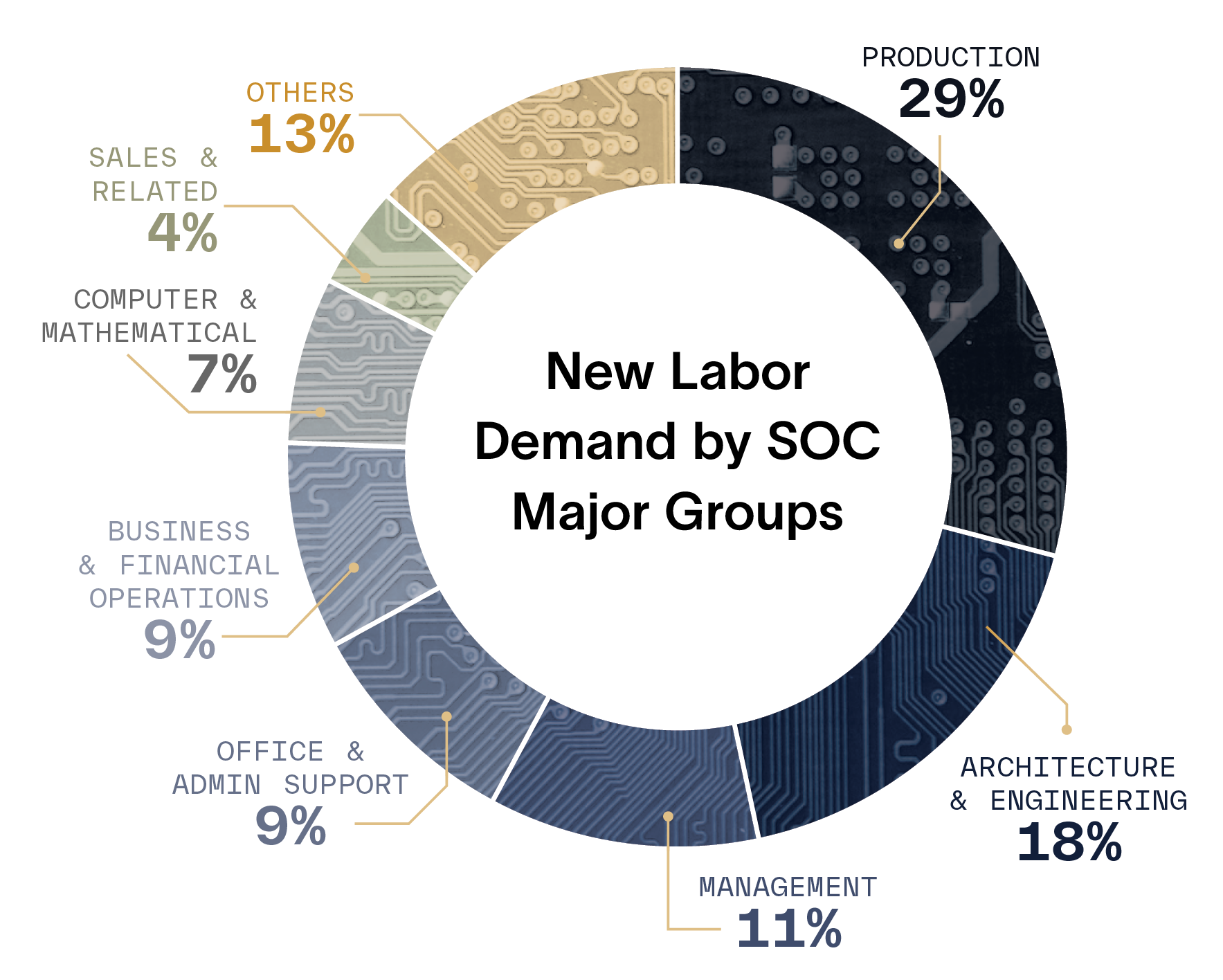
To arrive at the total jobs needed (236,878) and the occupational breakdown needed for a doubling of semiconductor production, the Lightcast Input-Output (I-O) Model was used. The I-O represents the flow of money in an economy, primarily looking at the connection between industries, and calculates the likely number of direct and indirect jobs resulting from an economic change—such as a new semiconductor plant.
Meeting the demand for semiconductors
To understand what types of occupations would experience the greatest demand, Lightcast compared the projected need to the projected supply of new workers into the roughly 236,000 new jobs produced from the I-O Model. Lightcast job posting data was used to represent the current demand for skills and project trends for future skill needs. By using graduates and workers who return to the labor force in the next 3-5 years, the current new supply was estimated.
To solve for undersupply and meet the demand need, the report distinguishes between reskill and redeploy occupations.
Reskill occupations are those that are undersupplied across the entire labor market. This means that the United States doesn’t have enough workers to fill the openings we have now, and certainly not enough to meet the additional demand that new semiconductor production will create.
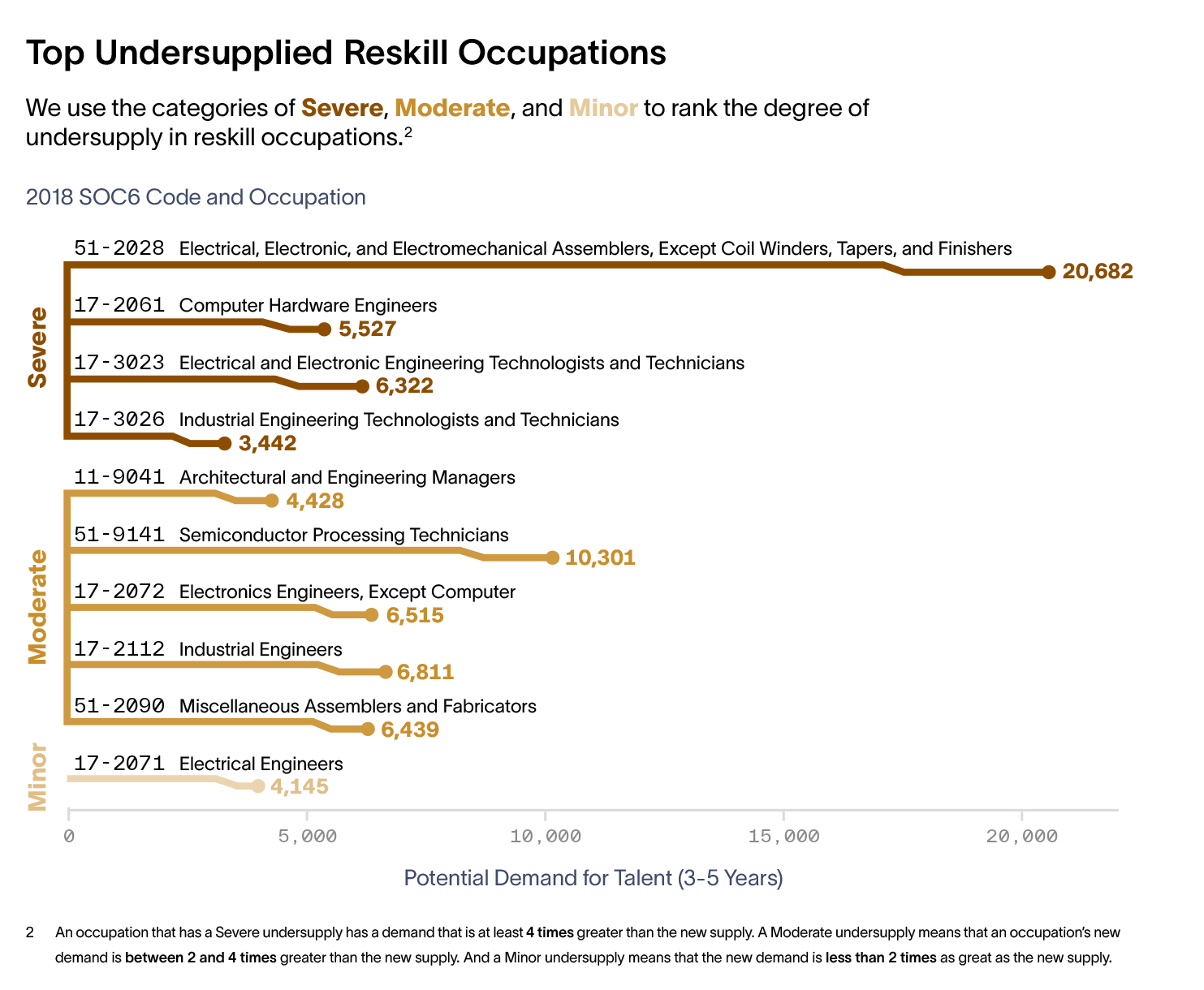
Redeploy Occupations are roles where there may be enough trained workers in the broader economy but not enough workers going into the semiconductor industry specifically. Workers in these roles have the necessary skills to work in the semiconductor industry, they just need to be recruited. And these redeploy occupations are for both degree and non-degree holders.

Rebuilding Our Semiconductor Workforce dives into ways communities can both reskill and redeploy workers to meet the semiconductor demand and take advantage of an industry that is set to expand rapidly. By knowing which jobs and skills will be in demand, and which regions and adjacent occupations have the greatest supply of workers, you can see how they align with the corresponding patterns in your industry—and where the gaps are.
Download Rebuilding Our Semiconductor Workforce: Making the Most of the CHIPS Act to learn more about the jobs and skills regions need to capitalize on this investment.