The newly-passed CHIPS Act is designed to revitalize US semiconductor fabrication, including billions of dollars designated for grants, research, and investment. Already, companies including Micron and Qualcomm have announced they will invest billions of dollars in expanding microchip production, leading to thousands of new domestic jobs in the industry.
But in a historically tight labor market, where will those workers come from?
First, some quick background. Semiconductors are essential to almost all modern technology: not just computers and phones, but cars, appliances, and a host of other uses. The United States’ share of global semiconductor production has fallen from 37% in 1990 to about 12% in 2022 as other nations have ramped up manufacturing. As recent supply-chain shortages highlighted, importing crucial components can lead to disruptions throughout the economy, especially because semiconductors are needed in the fabrication of other goods, as well as the manufacturing machinery itself. The CHIPS (Creating Helpful Incentives to Produce Semiconductors) Act is meant to address that vulnerability for both economic and national security reasons.
A study from the Semiconductor Industry Association and Oxford Economics projects that new federal investment will add 280,000 jobs to the US economy; 42,000 of which would be in the semiconductor industry directly.
But this growth presents a challenge: the long decline of US semiconductor manufacturing means that not many workers already have the necessary skills for these jobs. This is happening at a time when worker shortages are affecting the labor market at every level— especially workers with specialized skills like these.
In such a challenging environment for employers, the thousands of workers needed for semiconductor jobs won’t come from thin air. The quickest path to ramping up this workforce is to find employees who are already using similar skills in other roles across a variety of adjacent technical fields—this “skill adjacency” strategy allows workers to build on the skills they already have, providing the shortest possible training period for a new job.
Using Lightcast data, we can see which occupations and skills will provide the best fit for these semiconductor jobs.
We can start with defining what semiconductor jobs we’re looking for. Some are highly specific, like Yield Engineers, which are responsible for the technological aspects and dealing with line defects. Others—like Industrial Designer or Assembly Supervisor—are analogous to jobs in other complex manufacturing fields.
Since semiconductor manufacturing is so precise and complex, few workers are fully qualified to take new semiconductor jobs without additional training. But still, some occupations require less extra training than others—so those hiring for semiconductor jobs can start there in their search for the talent they need.
To use one example, Chemical Technician is one of the occupations most similar to Semiconductor Technician, given overlapping requirements for highly precise, scientific work. So while chemical technicians still need some “upskilling” to make the switch into semiconductor jobs, they’re still prime candidates for such a transition because they already have skills that both roles require, from knowing good laboratory and manufacturing practices to quality assurance and control.
More of these comparisons can be made using the Lightcast Skills Taxonomy, which uses our analysis of over 1 billion real-time and historic job postings and other data points to define what skills are required for which occupations. So while there are relatively few workers ready for semiconductor manufacturing in the US right now, our tools use skills to find and quantify workers whose skills position them well for those jobs. Workers in those skill-similar occupations can serve as “feeder” roles that would enable the easiest transitions into semiconductor work.
After finding who those workers are, we can also see where those workers are located—important for guiding staffing and development decisions for semiconductor investment. So while this influx of investment creates new opportunities throughout the country, Lightcast analysis finds many workers with “core” similarities to the semiconductor field are concentrated (relative to the general population) in the South and Midwest.
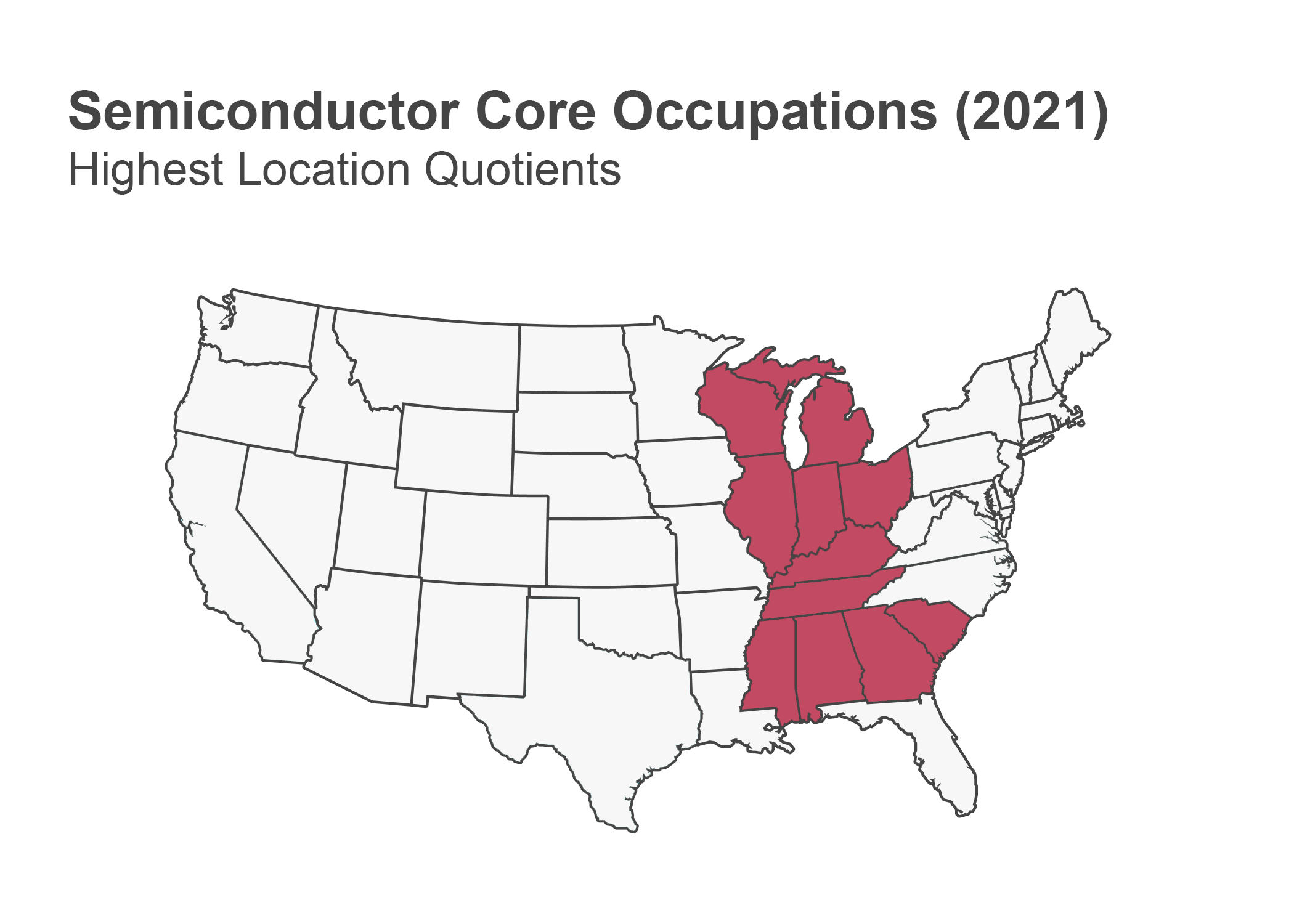
Expanding our focus to the adjacent talent pool with a lesser degree of similarity, the landscape changes slightly. While still concentrated in the Upper Midwest, we find that this new set of workers, which would need more targeted training and development, has a wider distribution.
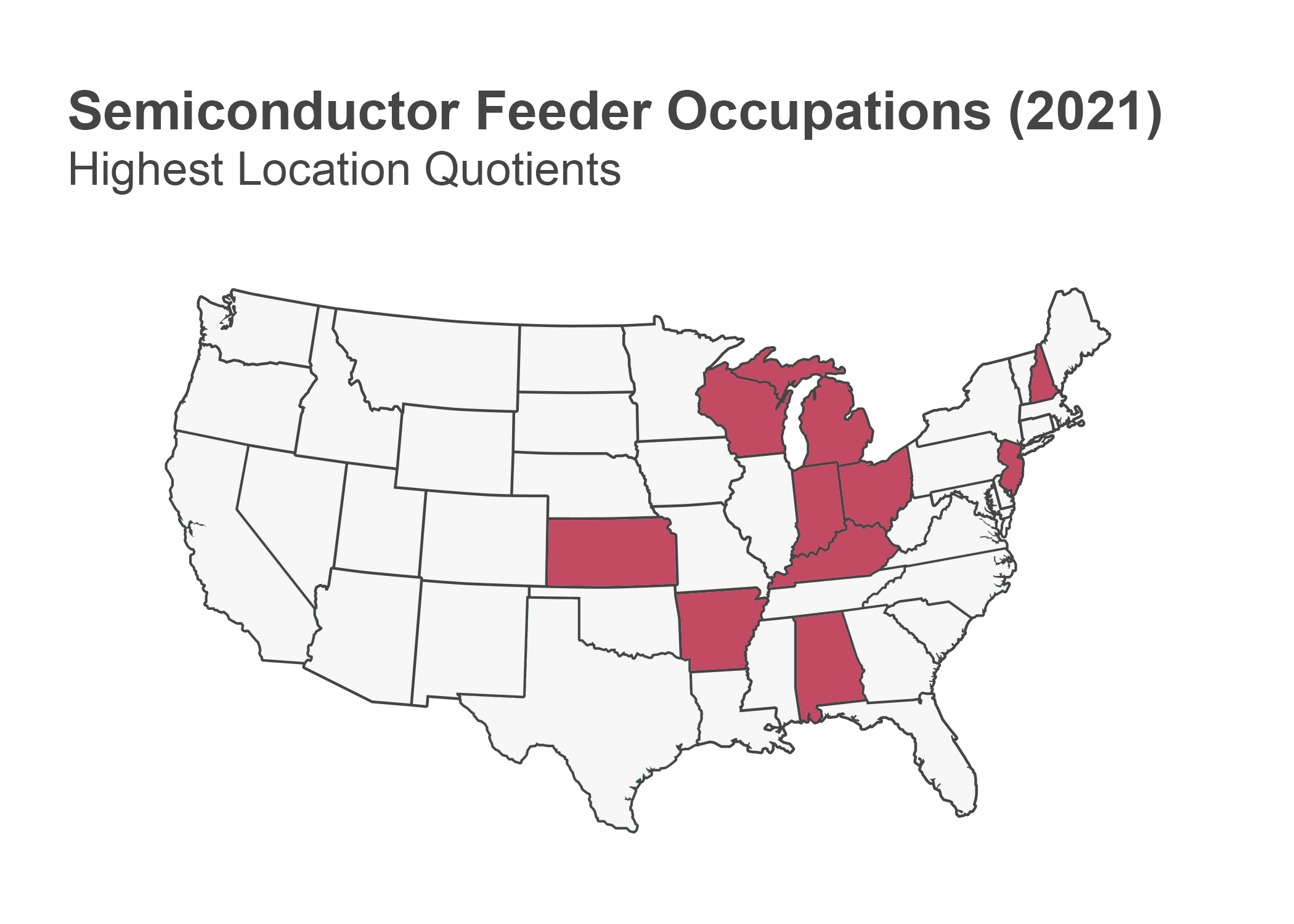
Any community vying to be a center of re-shored semiconductor manufacturing can benefit from understanding the strength of their current workforce and taking a closer look at how the skills needed in semiconductor manufacturing are already present in the regional economy. Current workers in the community might be distributed across a range of industries and occupations, and the connections between those jobs and semiconductor manufacturing may not be obvious, but they would still be a source of needed talent nonetheless.
Arizona, for example, doesn’t have a high concentration of semiconductor workers overall, but it does have a high concentration of occupations specifically related to electronics (including Electrical Designer, Electrical Controls Engineer, and Electrical Assembler). Indiana has a higher concentration of manufacturing and machinery jobs (such as Press Brake Operator and Production Machine Operator), while engineering jobs are more common in Maryland (including Aerospace Engineer, Biological Technician, and Hardware Engineer).
The domestic semiconductor industry is set to grow quickly in the next several years. And since the industry touches so many others, the impact of the coming investment will ripple throughout the economy and job market. This presents a business opportunity with a significant upside—and those positioned to take the most advantage will be those who can make the best staffing decisions, led by data-driven insight.