- Home
- Consumer Goods Manufacturing
Repackaging Skills in the Consumer Goods Manufacturing Industry
A future-ready consumer goods manufacturing industry has skills on the line.
Consumer goods manufacturing, or nondurable manufacturing, is largely production-based—meaning that hand labor is more prevalent than in durable manufacturing, which utilizes robotics and other technologies. This creates a particularly vulnerable subsector of manufacturing to labor market risks. Workforce shortages threaten production and quality continuity; coupled with growing supply chain challenges, these risks will continue to be harder to mitigate without strategic workforce intervention.
Risk Factors
2.79
Occupation Risk Score
Occupations focused on computers, data science, and software development are sparse in this industry. The most in-demand roles are overwhelmingly those that must be done by hand—first-line production supervisors, truck drivers, laborers and freight, stock, and material movers by hand, maintenance workers, merchandisers, distribution, and shipping, receiving, and inventory clerks. These are the very roles that are seeing prime-age workers exiting far faster than they are entering, especially among first-line supervisors, without technology roles integrating with operations to modernize production.
2.53
Market Risk Score
Consumer goods manufacturing spans a wide range of locations. Many US food companies are well established in rural, suburban, or small-metro communities and part of local history, resulting in a stable supply of prime-age workers. Conversely, products like candy, beverages, and cosmetics also have long-standing operations across Europe, benefiting from populations who have maintained brand affinity as well. These companies, and apparel and home furnishings manufacturers, also establish operations where source materials are located—which benefits local workforce sourcing, but can also present supply chain risks.
4.00
Industry Risk Score
Consumer goods manufacturing must seize opportunities to develop the local workforce. While foreign-born workers have sustained this labor force, geopolitical uncertainties cannot guarantee that this population can continue to stabilize shortages, especially in an industry that has had an over-relience on immigration. Manufacturing as a whole has globalized operations for many years; however global supply chain challenges have already threatened operational stability. While AI, robotics, and automation have made strides in optimizing production lines, many consumer goods still rely on manual labor.
2.24
AI Skills Gap Score
While corporate roles such as executive leadership, financial specialists, data analysts, and marketing positions are heavily exposed to current and emerging AI skills, frontline workers are not. As technologies advance in material movement, production lines, quality testing, and logistics, employees in these roles need to undergo skills transformation. The technologies that can alleviate workforce shortages require skills that the very workforce most in need of bridging the gaps lacks. However, leaders must drive AI adoption strategies that engage frontline workers, rather than cause concern of job displacement, by valuing their input and production expertise.
Consumer Goods Manufacturing Organizations in the Fortune 1000
In the Workforce Risk Outlook, Lightcast found little correlation between workforce risk exposure and their Fortune 1000 ranking. C-suite leaders must align their workforce strategies with their quadrant position, as opposed to assuming their revenue makes them immune.
High Risk/High Scale to Address: Organizations in this quadrant face significant risk of being disrupted in their industry, but also have the financial resources to reduce their risk if they are proactive. These organizations should reduce risk by increasing automated production line technologies and adopting market flexibility to source talent and enhance supply chain efficiency.
High Risk/Lower Scale to Address: Organizations within the riskiest quadrant are lower on the competitive ladder and have less resources to address their incoming risk. These organizations must prioritize lean manufacturing, multi-skilled labor, and explore strategic partnerships with suppliers to create more resilient production networks.
Lower Risk/High Scale to Address: Organizations in this quadrant may not face immediate workforce shortages, but should remain proactive to maintain and reduce their exposure to risk. Expanding automation while upskilling employees in data analytics and robotics can sustain productivity and help mitigate future labor shortages.
Lower Risk/Lower Scale to Address: Organizations in this quadrant, if they are proactive, have a chance to be the disruptors. Specifically, they can disrupt industry competitors in the High Risk/High Scale quadrant. These organizations should focus on evolving consumer demand, rapid production cycles, and strategic talent development to capture market share from less adaptable competitors.
See the Full Fortune 1000 List by Lightcast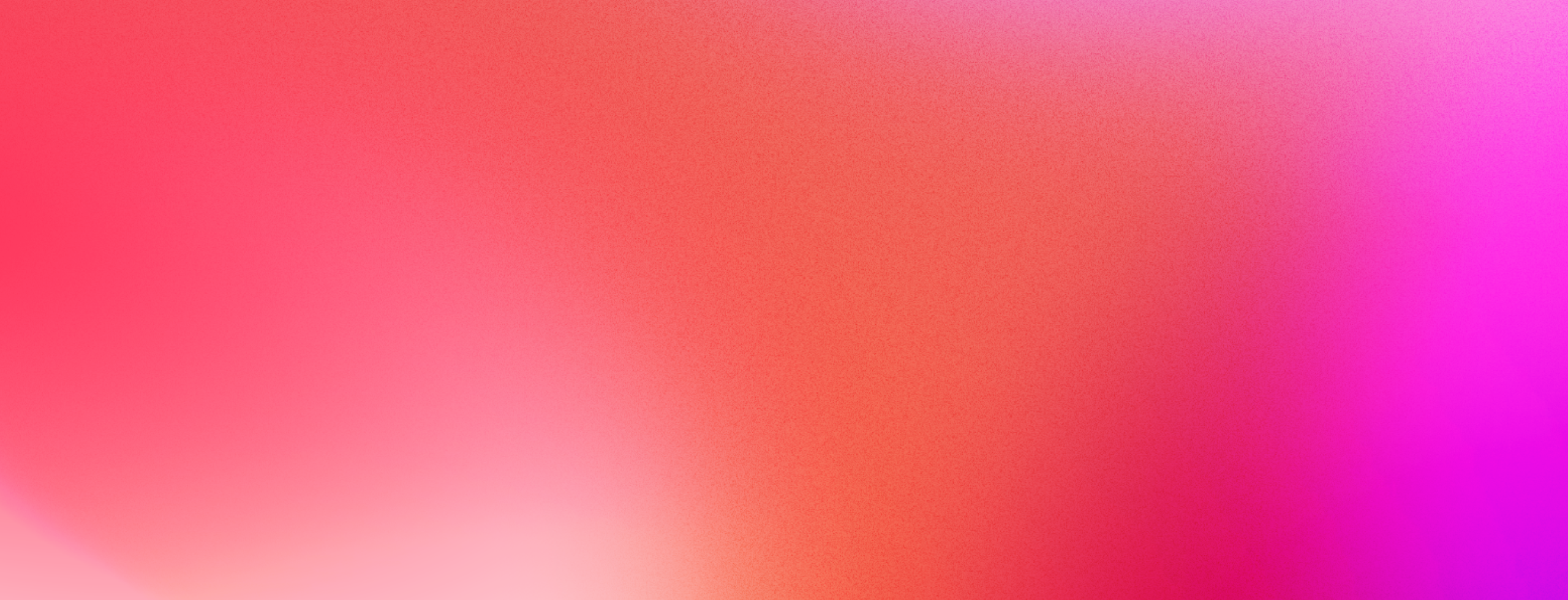
Ready for Lightcast to prepare you for the storm?
Solving Consumer Goods Manufacturing Workforce Management
Talent Analyst
Strategies to Expand Global Markets Using Talent Data
Though globalization is a key relief for workforce gaps, expansion efforts must be planned carefully to ensure talent is in place for all workflows along the supply chain. Products must be made, and go to the markets where they are sold. Organizations must conduct comprehensive labor market analysis for talent availability, wage competitiveness, and demographic trends to target expansion regions. Aligning business needs and workforce planning requires identifying critical roles, and developing strategies to retain local talent to ensure their new operations are positioned for sustained growth and efficiency.
How Apparel Manufactures Expand Around the Globe
A global leader in sportswear continues to expand across the globe, requiring data to make sound market decisions. Using Lightcast’s global market data, the manufacturer is equipped with a comprehensive understanding of labor markets, compensation trends, and the availability of both skilled and underutilized talent across the UK, Eastern Europe, Latin America, and more. These insights have informed methodical expansion and talent transformation strategies to strengthen its ability to plan for the future, address talent gaps, and build a workforce that reflects its values and business priorities.
Talent Transform
On-the-Job Training Strategies to Attract the Next Generation
The industry must prioritize upskilling and reskilling workers to adopt automation, data analytics, and digital manufacturing in order to ensure capacity to keep pace with market demand for goods. Internal programs, apprenticeships, and paths to on-the-job certifications are essential to fill roles where tasks cannot be automated. While many manufacturing subsectors are able to offshore or nearshore production, global shifts in supply chain still presents risks to operational continuity; manufacturing companies must ensure they can secure and maintain a core local workforce to respond to these shifts.
How Food and Beverage Companies are Revitalizing Careers
A Fortune 100 food and beverage manufacturer is collaborating with Lightcast to mature a skills-based framework built for future business demands. By mapping job titles and skillsets to industry standards, refining role-specific skills lists, identifying transferable skills, and expanding its skills taxonomy across global markets, it has bridged skills gaps and is prepared for skills change. With skills as the focal point of workforce planning, and as a key driver in operational strategy, it is equipping its teams with the tools to remain competitive, foster employee growth, and evolve with market expectations.
