- Home
- Manufacturing
Assembling a Future-Ready Manufacturing Workforce
The products in this manufacturing industry are durable, but is its workforce?
The manufacturing industry faces substantial pressures to businesses’ operational ability and market demand delivery. Workers are in critical shortage, the skills gap is widening in advanced technologies—especially as robotics, nanotechnologies, and biotechnology advance—and specialized talent is in high demand. Manufacturing leadership must invest in upskilling, attracting younger talent, acquiring skills-adjacent tech workers, and leveraging automation and automation-skilled employees.
Risk Factors
2.06
Occupation Risk Score
While one of the top occupations in this industry is software developers, which has a stable prime-age working population, critical roles specific to durable manufacturing, like front-line supervisors of production and operating workers, industrial engineers, inspectors, and maintenance and repair workers, will continue to see high exits of retiring workers. Without quickly advancing the skills of the current prime-age workforce in these roles, the industrial knowledge needed to secure business continuity is at risk of evaporating. Companies need to retain these workers and ensure a transfer of knowledge from those approaching retirement in order to sustain and grow.
2.56
Market Risk Score
Cities in the Midwest United States continue to carry the manufacturing tradition with plants located in Chicago, Ill., Detroit, Mich., Columbus, Ohio, and Minneapolis, Minn. However, these areas are also experiencing high rates of prime-age workforce exits as people reach retirement age, which will continue throughout the next 10 years. Many manufacturing operations are also located in small towns. While there is still a moderately high risk of the available workforce aging out, some areas, such as Elkhart, Indiana, have populations with cultural roots in manufacturing. Companies must create a workplace culture of pride and career growth to obtain and retain their employees.
4.00
Industry Risk Score
The durable manufacturing industry can expand its workforce through local workforce development, immigration, globalization, and automation, moderately mitigating risks. Computer, automotive, and machinery subsectors have led the way for automation, and have been offshoring the longest of any industry. However, recent global supply chain issues are creating offshoring challenges, and geopolitical conditions present many unknowns with the foreign-born workforce as a sustainable source. As technologies rapidly advance to optimize worker capabilities, durable manufacturing companies must focus on AI, automation, and robotics, especially related to production design.
1.82
AI Skills Gap Score
While automation is rapidly growing in manufacturing and a lever that can alleviate talent shortages, workers will need the skills to adopt, manage, and maintain automated systems. Additionally, the growth in high-tech manufacturing requires data analytics that can be applied to optimize production, quality control, and supply chain management. These roles are being highly exposed to AI skills, helping to modernize the workforce. However, roles in assembly, production workers, maintenance workers, and material movers—all of which are in severe shortage—are much less exposed to AI skills, leaving unrealized opportunities to fill gaps with these technologies.
Manufacturing Organizations in the Fortune 1000
In the Workforce Risk Outlook, Lightcast found little correlation between workforce risk exposure and their Fortune 1000 ranking. C-suite leaders must align their workforce strategies with their quadrant position, as opposed to assuming their revenue makes them immune.
High Risk/High Scale to Address: Organizations in this quadrant face significant risk of being disrupted in their industry, but also have the financial resources to reduce their risk if they are proactive. These organizations should invest in large-scale reskilling programs, expand robotics and AI-driven production lines, and establish partnerships with technical schools to secure a steady pipeline of skilled labor.
High Risk/Lower Scale to Address: Organizations within the riskiest quadrant are lower on the competitive ladder and have less resources to address their incoming risk. These organizations must focus on lean manufacturing principles, automate repetitive tasks to reduce dependency on manual labor, and explore supplier diversification to mitigate production disruptions.
Lower Risk/High Scale to Address: Organizations in this quadrant may not face immediate workforce shortages, but should remain proactive to maintain and reduce their exposure to risk. Investing in smart factories, expanding sustainability initiatives, and offering upskilling opportunities in digital manufacturing technologies will help future-proof their operations and workforce.
Lower Risk/Lower Scale to Address: Organizations in this quadrant, if they are proactive, have a chance to be the disruptors. Specifically, they can disrupt industry competitors in the High Risk/High Scale quadrant. They should invest in additive manufacturing (3D printing), explore customizable production models, and implement digital twin technology to optimize efficiency and attract a highly skilled workforce.
See the Full Fortune 1000 List by Lightcast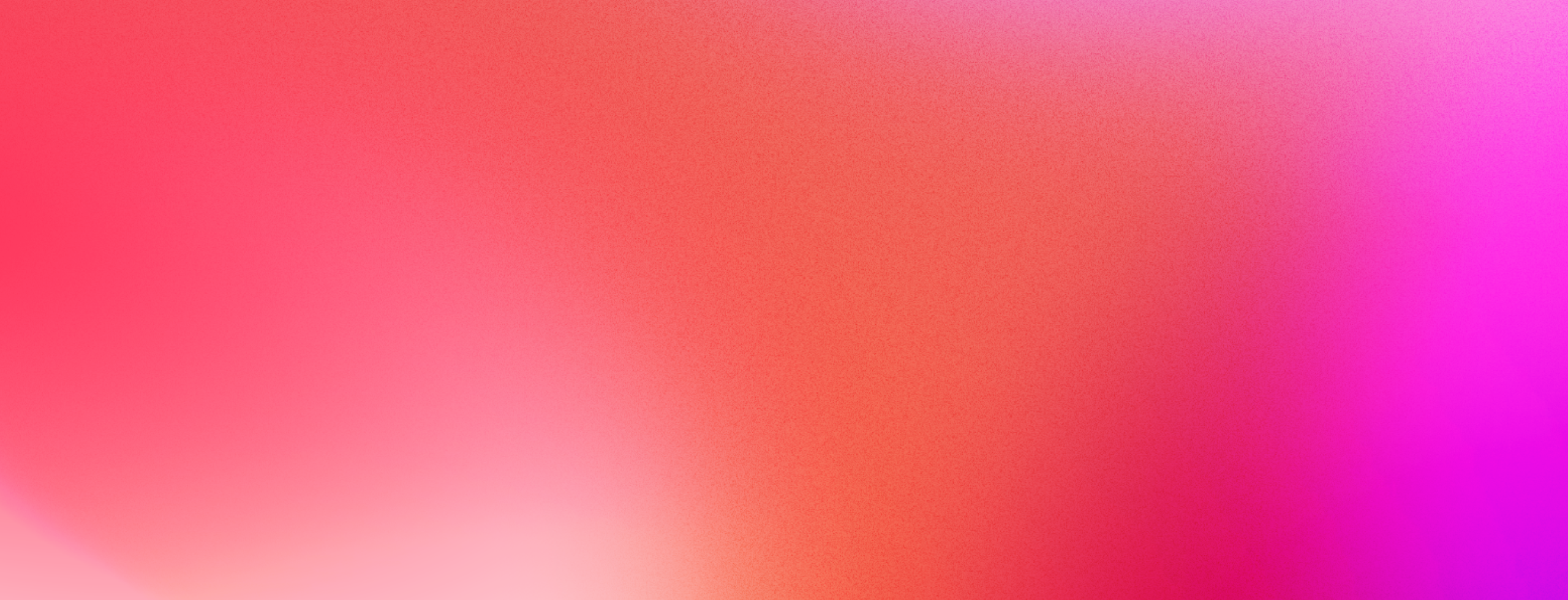
Ready for Lightcast to prepare you for the storm?
Solving Manufacturing Workforce Management
Talent Analyst
Strategies to Engage an Underutilized Manufacturing Workforce
Manufacturing leaders must focus on expanding the talent pool and retaining workers in order to meet production demands. Reengaging with the underutilized workers and reskillable roles are critical. With insights on the available workforce—unemployment rates across geographies, young people approaching working age, alternate paths of education, women, adjacent skills, and foreign-born workers—manufacturing companies can unlock underutilized talent pools and attract these workers with competitive career paths and compensation to gain and sustain their talent.
How Durable Manufacturing is Expanding Its Talent Pool
A leading appliance manufacturer is addressing talent acquisition challenges by integrating Lightcast’s comprehensive labor market data into recruiting and workforce planning strategies. Focused on reaching underutilized talent pools with actionable insights, this data has illuminated workforce demographics, including diversity, education, and regional talent trends to refine hiring strategies for critical roles like project managers and engineers. It is achieving both its diversity goals and ensuring a strong talent pipeline, investing in career growth that strengthens its operating regions.
Talent Transform
Strategies to Be AI and Automation Ready
AI, automation, and advanced robotics are transforming the durable manufacturing workforce. To stay ahead of emerging skills, analyzing job postings and identifying disruptive technical skills, along with interpersonal durable skills, like problem solving and agile methodology, can drive strategies to map career paths, upskilling, and cross-functional teams. Leveraging tools such as learning management systems and talent analytics platforms enables companies to integrate real-time labor market insights and customize career pathways that lead business transformations of the future.
How Manufacturing Can Develop Future-Forward Skills
A Fortune 1000 semiconductor manufacturer sought to identify and develop the critical skills and capabilities needed for its roles of the future, including advanced robotics operators, engineers, and network architects, is growing its workforce capabilities and AI skills. With Talent Transform, curated role profiles and job market analytics are driving a robust competency framework for solutions engineers and other innovation roles. By streamlining talent acquisition, development of emerging skills, and building a scalable talent intelligence strategy, it continues to solidify its position as an industry leader.
